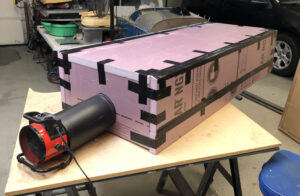
My Composite Cure Box
I learned in the past and was reminded this past early spring that composite layups do not cure very well in cold temperatures. For that matter, the layup process also needs fairly warm temperatures or the epoxy gets thick and unworkable.
While I can heat my garage upwards of 65 degrees when it’s below freezing outside, it’s not good enough for curing.
To overcome the cold winter conditions here in Iona Idaho, I have built a temperature controlled heat box to keep my epoxy ingredients at a constant 80 degrees. That together with the 65 degree garage temp will enable me to do smaller size, simple quick layups. But its still not good enough for curing.
So I built a foam box with an electric heat source that I can run overnight to better cure parts even when the garage temperature hover around 35 to 40 degrees.
I built the box 6 ‘ long, 2’ wide, and 14″ tall out of 1.5″ thick insulating foam you can get from your local home improvement store. I used resharpened 16 penny nails to temporarily hold it together then applied duct tape to secure it. The box size was determined to fit the largest part which is my floor pan mold. Anything else will be smaller until I build me my all composite Bugatti Type 59.
The box is constructed so it only has five sides. I intend to put my part/mold onto a foam sheet bottom; in this case only 1/2″ thick because that’s what I have laying around. I then drop the foam box on top, connect up the heater, and turn it on.
The electric heater is circular in shape and has it’s own temperature/thermostat. It just happens to fit an 8″ piece of stove pipe to direct the air into my curing box.
When not in use, I simply pull out the heater/pipe and store it away in a corner of my shop. I may cut the tape after I’m all done to enable me to fold it into a flat shape to take up even less space. We’ll see.
I have multi-meter with a temperature probe so I will monitor the interior temperature initially to see how best to set the heater controls. I want to get about 90 degrees inside which should cure my parts very nicely.
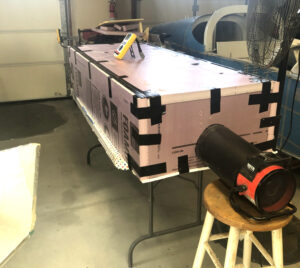
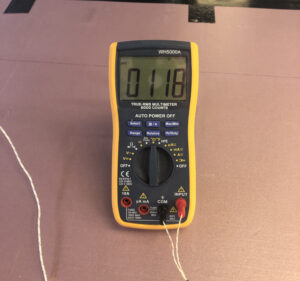
Nov 10
I did my first fiber glass layup today as a trial run for my composite curing box under cold winter conditions. It was very cold wintry conditions outside and it took a long time for my ceiling mounted heater to get my three car garage up to about 70 degrees. Unfortunately, my epoxy temperature controlled storage box had stopped working for reasons unknown so the resin was so stiff the pump did not work. I had to pour the stiff resin directly out of the can. It was still thick, so I employed my electric heater and directed it to the mixed epoxy which did a pretty good job of thinning it out.
The first piece I fiber glassed was the seat back. This is as simple as it gets and I did the layup on my glass window table top. Unfortunately it too was cold and so the epoxy did not like penetrating the fiber glass cloth on top of the cold window glass. It wasn’t until I used the auxiliary electric heater to thin out the epoxy and warm up the glass/work table that things proceeded normally. Lesson learned.
The curing box with the heater did a marvelous job at holding the temperature inside 110 to 118 degrees. The heater thermostat driven by the temperature outside the box did not do a real good job. So I found a setting that basically stabilized it to within this range. I have ordered a temperature controller with its own probe to control the power to the heater so I can keep it controlled to an exact temperature under any external temperature condition. I will use that on my next layup next week.
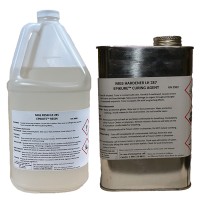
Nov 11,
I got up early and went into the garage to make sure my curing contraption had not caught on fire. Fortunately it was still working and purring just beautifully even though the temperature inside the box was only 88 degrees. That was most likely because our high today was only going to be 25 degrees outside and the garage had dipped into the 30’s.
When I disconnected the heater and removed the insulated box I inspected my part. It was hardening, but still soft which was a little concerning. I would have hoped it would have been cured by now. Further inspection revealed some edges had peeled up off of the 1/4″ foam which was disappointing. It was then that I recalled having used weights in the distant past to prevent this from occurring. Another lesson was relearned.
Earlier this year I purchased resin and epoxy from a supplier I had never used before because their pricing was the very best around. I was very pleased with the quick shipping and quality of the fabric, but this resin and hardener are just not working for me. So I am chucking it and going back to MGS L285 resin and the 340 slow hardener. It has always worked very well for me in the past and again more recently this summer. Another lesson learned.
I’m glad I did this test project first before attempting the more complex floorpan. Had I just jumped into the floorpan I think I would have gone very bad.
I am looking forward to receiving the temperature controller and resupplying my MGS resin and hardener. Both should arrive next week.
So I will call this project a great success and move on to the next.
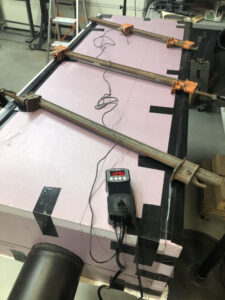
Nov 19
My temperature controller, a new quart of hardener, and rolls of fiberglass showed up this week so I was ready for an actual layup.
I covered the backside of the radiator with three layers of BID fiberglass and then covered the radiator with the composite curing box. I next plugged in my new temperature controller. I liked the construction of the controller, but I had to read the instructions to get the correct sequence of button presses to set the On and Off modes. I set the On to 120 degrees and the Off to 125 degrees. It has worked flawlessly and kept the box interior precisely between 120 and 130 degrees independent of the garage workshop temperature. I learned that even though the unit shuts the heater off at 125 degrees, the temperature continues to climb to 130 degrees anyway but then over the course of 5 – 10 minutes falls back down to 120 degrees. So it cycles pretty frequently, but the on-time is pretty minimal compared to when I was basically running it 100% of the time at a lower heat setting. I find this setup is perfect; I am very pleased with the result.