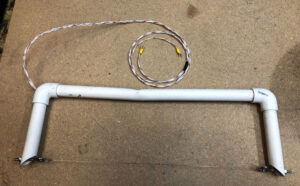
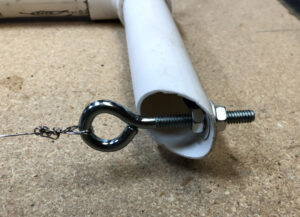
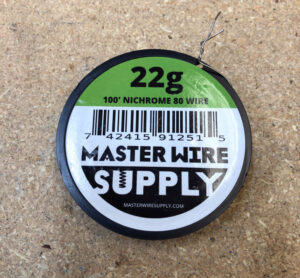
Building a Hotwire Foam Cutter
Hot wire foam cutters apply electrical current through a tightly strung monchrome wire making it very hot. When slid along a template such as my radiator shape or a wing rib, it slices through foam like a hot knife through butter.
While one can always simply carve the foam to the desired shape without a hotwire cutter, anytime you have a very specific shape or need to produce multiple foam pieces that are all identical, the hotwire foam cutter really pays off.
In my case, it’s only one item and I could easily have carved and sanded it to the desired shape, but I already had the wood bucks so why not? It will make it so much easier.
The build is very simple. I used 1″ PVC with 90 degree elbows at each end.
Eyebolts were attached at either end that accepted one wire from the power supply and also was used to string the monochrome wire. I used 22g monochrome wire I bought from Amazon.
I had a variable electrical power supply I used for some crazy idea experiments of the past laying around so I planned on using it to provide the 12V at 5 amps. Unfortunately, it would not go that high so I bought one from Amazon.
The wires run inside each end and come out together at one end and make their way to the power supply. The monochrome is stretched across the back-prebowed 1″ PVC. I heated it with a heat gun while bowing it backwards. Be careful not to heat it up to much or you will get a kink like I did. I caught it quickly though and let it cool, so no real damage was done. That way when you attach the monochrome wire, pull it real tight so the PVC frame straightens itself out thereby keeping tension on the wire. This guarantees the best and most true cut when following your template.
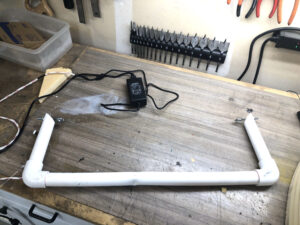
Nov 11
My new power supply arrived today so I was eager to plug it in and get on with it. But of course, nothing goes according to plan.
Once connected, it started to work but then stopped. I was puzzled and decided the pin connector on the power supply was at fault, so I cut it off and hardwired the power supply directly to my foam cutter wires. I did it all properly with solder, heat shrink sleeves and then wrapped it in wire tape. While I was at it, I cut off the monochrome wire, and restrung a new piece on with much greater tension.
When I plugged it in this time, everything worked as planned. You can smell the burning wire as it heats so you know it’s working. The foam gives off very harmful fumes so I put on my respirator for good measure.
The cutter worked well enough, albeit not as quickly as I had expected. I found I had to move the hotwire up and down to get it to move along the template. In all honesty, I could have just whacked off the excess foam with my knife and then sanded down the foam in far less time than it took to build this contraption and perform the cut on my radiator project.
I had built a hotwire foam cutter about 30 years ago, and it seemed it worked better then. But I wasn’t cutting through three-inch thick foam back then so that might be why it went slower.
Once again, I reminded myself, I am doing this for the learning experience. I believe there will be plenty more opportunities to cut more parts, so I am still glad I built this so it’s plug-in ready for the next project.
So I’ll call this a success and move on.